多品種少量生産に関する各企業の取組み
BtoBの機械系製造業では、グローバル市場で勝つためのカスタマイズ化・高付加価値化を目指し、それに伴って発生する課題解決に取り組んでいます。
製品が多様化して一種類当たりの数量が減り、機能や形状(精度)が高度化するに伴い、いままでの大量生産方式から多品種少量生産、小ロット・タクトタイム違いの生産対応などへの動きが始まっています。今回コラムでは、いくつかの日本の製造業において実際に各企業が直面した課題・背景とそれに対する取り組みについてご紹介いたします。
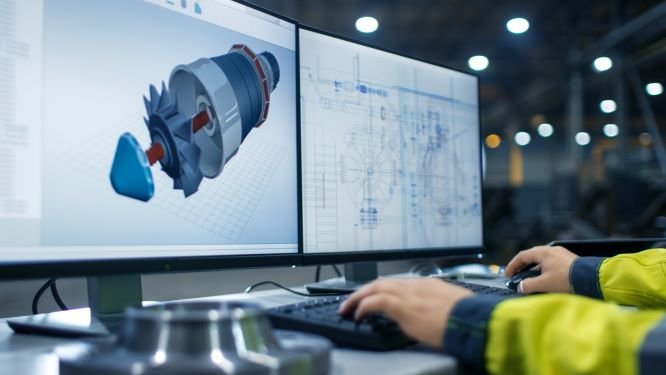
日本の製造業における取組み事例
油圧機器製造業(A社)
A社は油圧機器事業、板金加工事業などを展開している中小企業だ。2008年に起きたリーマンショックは、同社の経営に大きな影響を与えた。
これをきっかけに同社は、今までのビジネスモデルでは経営が成り立たないことに気づき、ビジネスモデルの変換を試みた。それは従来のビジネスモデルからオーダーメイドで高付加価値を提供するビジネスモデルへの移行だ。
しかし、このシフトは社内の各組織に多くの困難をもたらすものだった。例えば、個別受注への対応力不足、業務負荷の集中、そして納期の遅れなどの問題が発生した。この問題を同社の経営層は、深刻な経営の危機と捉え、現場との意見の交換を重ね、その結果問題を解決するためにはデジタルシフトへの取組みが必要不可欠であるという結論に至った。
過去の同社は、特に設計面においては、現場頼みの運営であったが、現場では図面のやり取りはすべて紙媒体で行われていた。それに加え、外部環境の変化によって生まれた新たなビジネスモデルの実現にむけて、更に業務プロセスの複雑さを増していった。
そこで同社はこの課題解決のために、業務プロセスの最適化と社内連携体制の可視化に着手した。たとえば、これまで現場依存であった設計部門に対しても改革を行った。課題であった紙による図面設計を、最新の3DCAD をはじめとする最新のツールを導入し、設計と調達、設計と製造のやり取りを繋ぐシステムの導入も行い、改善を図った。
業務にデジタル化を進めたことで、既存の事業の位置づけを変えるだけではなく、着手が進まなかったビジネスモデルの変革にも取り組むことができ、コスト削減を実現するとともに、事業の高付加価値による売上の増加にも貢献ができた。
一方でデジタル化による新たな取り組むべき課題も見つかった。それはデータを資産としてどう活用するのか、そしてデータ間の連携をどう実現するのかという点である。具体的には3DCAD による設計データ資産の再利用と流用設計、そして工数見積力の強化、顧客や仕入先とのデータの連携などである。
今後はそういった課題を解決するためにBOMや BOP といったシステムの導入の検討を重ね、またそのデジタルツールを扱える生産技術者を中心とした人材への支援と育成が必要不可欠だと考えている。
社会インフラ制御機器製造業(B社)
社会インフラを支える情報制御システム提供しているB社は、顧客からの要求・用途に多品種少量生産で対応している。
同社は顧客の個別仕様に対するきめ細かさに強みを有している一方で、グローバル競争におけるスピード面とコスト面で課題を抱えている。同社は強みを維持しつつグローバル市場でも勝ち続けるために、以下の3つの戦略を掲げている。
- 需要変動に速やかに対応
- 顧客要求に応えた高付加価値の製品を提供
- 大量生産製品と同等の価格競争力
これを実現させるために、B社は次世代システムの開発に取組んでいる。このシステムのコンセプトとして2つ掲げている。
1.生産能力把握の精度向上
B 社が取り扱う製品は、多品種少量生産(オーダーメイド品)である。製品群においてはある程度の類似性が見られるが、大半は一品一様に設計され、生産された製品である。そのため、製品ごとにリードタイムにばらつきが生まれ、量産品と比較した際の生産能力の把握に課題を抱えている。その課題を解決するためには、生産プロセスにおける動態情報や作業進捗情報を精査し、生産現場を正しく把握することだと考えている。
2.生産情報の連携(垂直方向連携・水平方向連携)
従来、同社の生産改革活動は、多品種少量生産を効率的に行うことに注力していた。そのため、製品ラインアップごとに業務システムやプロセスの個別最適化が進んでいた。その結果、情報同士のつながりが不十分で、蓄積・利活用が困難な情報が多く存在し、不揃いな情報が部門間・工程間の連携を阻害していた。例えば、過去の経験によって蓄積されたノウハウや失敗事例といった情報は、部門間や個人の中だけで留まっており、担当者の変更を繰り返すうちに世代間の技術伝承が十分に行えなかった。
その課題を解決するため、各部門が持つルールやノウハウ、そして過去の事例を全てデジタルデータ化し、全社で共有を推進した。さらにデジタルデータ化した情報を、構造設計システムである3DCAD上でも参照可能とし、不良作り込みのリスクを設計の段階から低減する仕組みを構築した。これにより、手戻り作業を事前に防ぎ、コストの削減に成功している。
また、同社は日本での実績をもとに、今後海外拠点も含めた情報の利活用と可視化の実現を目指している。
通信機器製造業(C社)
C社は、情報通信、メカトロシステム、プリンター分野を中心とした事業をグローバルに展開しているが、最近では従来のものづくりに限界を感じている。その理由は主に二つで、市場ニーズの変化と得意先からの要求の多様化である。
同社は、個々の事業に特化した工場をはじめとする生産体制と活動を行っており、各事業の設計部門が出す仕様に基づいて生産体制と設備が最適化されている。従って各工場においては、事業内容に応じて仕様から生産までの考え方、プロセスが異なっている。そのため、ある工場において、別事業の製品を柔軟に生産することが難しいといった課題を抱えていた。
そこで同社では、生産と品質の改革を目的とした「バーチャル・ワンファクトリー」活動を実施し、複数の工場間を仮想的に一つの工場として結合し、その仮想空間内で得意先から求められる要求への対応や人手不足を緩和するための負荷分散を図った。さらに、外部環境の急激な変化に対しても柔軟に対応できる体制づくりを目指した。
現在では、生産プロセスの上流を担う設計部門を巻き込んで全社活動を展開中である。今後は個別最適から全社最適を求め設計、生産だけではなく調達を含め全体の標準化を進め「バーチャル・ワンファクトリー」を実現したいと強く考えている。
自動車用部品製造業(D社)
自動車部品の組付工程を行っているD社は、かんばん方式によって必要な時に必要な数量を効率的に生産している。
同社の強みは、大ロットを高速加工する大量生産であり、その強みで競争力を維持してきた。 その競争力の源は、製品に組み付けられる部品の加工分野における、段取りや設備稼働率を優先して取り組んできた点である。
しかし、従来メリットのあった大量生産による方式では無駄が多く発生するようになってきた。その背景は、製品が多様化し、一種類あたりの数量が減ったこと、そして機能や形状(精度)が高度化したことにより、単独の加工のみで部品が完成することが少なく、新たな切削・熱処理といった多くの加工分野を経て部品が完成するようになったことにある。
この環境変化に伴い、同社は加工費低減を推進するためにある取組みを行った。それは、複数の工程にまたがる労務費と償却費を加えた加工費の低減を推進するために、徹底的に無駄を取り除いた同期一貫ラインの実現である。
そのポイントは、人の関わりを最小限として、労働価値を高めること。そして加工ラインの小型化とシンプル化させることであり、実現するためには、すべてのムダ(材料・副資材のムダ、大きさのムダ、搬送・動作のムダ、在庫のムダ)を取り除くことである。具体的には、従来の大量生産の論理で導入した大規模な生産設備体制を、ロットサイズ、タクトタイムの違いに合わせて最適化できる生産量の適切な設備に置き換えた。これにより、加工段取りのしやすさが生まれ、保全性の向上、省資源化・リードタイム短縮に大きく貢献した。
今後は、上記の点を踏まえ、グローバル生産展開の中で、より早く供給することを目指している。
今後の取組みに向けて
今回ご紹介した4社は事業および製品形状は異なりますが、いずれもグローバル化・市場ニーズの変化などにより危機感を覚え、高付加価値化につながる多品種少量生産をより効率的に実現すべく、現場視点で課題を明確にし、それぞれ具体的な取り組みをされています。
製造業においては「変化に強いものづくり」の実現こそが、昨今の「不確実性の高まる世界」において求められる企業変革力(ダイナミック・ケイパビリティ)を高める第一歩となるはずです。
関連サービス
-
インプリメンテーション
ERPソリューションを中心に据えながら、デジタルトランスフォーメーション(DX)を実現するための基盤や関連する業務システムとの連携、データ活用など、お客様の課題を解決するためにシステム特性を理解したプロフェッショナルがご提案します。
関連資料
-
不確実な時代に応える変化に強いものづくりの実現
多くの製造業が抱える大きな課題として「不確実性の高まる世界」への対応が挙げられます。
こうした先を見通すことが難しい時代だからこそ、「変化に柔軟に対応できる強いものづくり」の実現が強く求められます。そこで、NTTデータGSLは今まで部分最適で行ってきた「設計と生産」に着目し、その両者の壁を解消に、いかにコストを抑え、そしてスピーディに生産と設計の連携を深める、不確実な時代を勝ち抜く「データに基づくものづくり」の実現を提案します。 ダウンロード -
多品種少量生産の受注設計生産型製造業
多様化する顧客のニーズやグローバル化により、受注設計生産型の製造業では多品種少量生産のマスカスタマイゼーションが求められています。 多品種少量生産に対応しようと努める企業の多くが、顧客のニーズをモノづくりにどう反映させたらいいのか、とくに設計プロセスと生産プロセスの連携、製造プロセス全体の最適化に課題を抱えています。 そこでNTTデータGSLは、設計と生産のシームレスな連携を実現する受注設計生産型製造向けのソリューションをご提案します。 ダウンロード